Trong những năm gần đây, nhờ sự phát triển nhanh chóng của ngành năng lượng mới, hàn laser đã nhanh chóng thâm nhập vào toàn bộ ngành năng lượng mới nhờ ưu điểm nhanh và ổn định. Trong số đó, thiết bị hàn laser chiếm tỷ lệ ứng dụng cao nhất trong toàn bộ ngành năng lượng mới.
Hàn lazeđã nhanh chóng trở thành sự lựa chọn hàng đầu trong mọi tầng lớp xã hội nhờ tốc độ nhanh, độ sâu lớn và biến dạng nhỏ. Từ mối hàn điểm đến mối hàn giáp mép, mối hàn đắp và hàn kín,hàn lasercung cấp độ chính xác và khả năng kiểm soát tuyệt vời. Nó đóng một vai trò quan trọng trong sản xuất và chế tạo công nghiệp, bao gồm công nghiệp quân sự, chăm sóc y tế, hàng không vũ trụ, phụ tùng ô tô 3C, kim loại tấm cơ khí, năng lượng mới và các ngành công nghiệp khác.
So với các công nghệ hàn khác, hàn laser có những ưu điểm và nhược điểm riêng.
Lợi thế:
1. Tốc độ nhanh, độ sâu lớn và biến dạng nhỏ.
2. Hàn có thể được thực hiện ở nhiệt độ bình thường hoặc trong các điều kiện đặc biệt, và thiết bị hàn rất đơn giản. Ví dụ, chùm tia laser không trôi trong trường điện từ. Laser có thể hàn trong chân không, không khí hoặc môi trường khí nhất định và có thể hàn các vật liệu xuyên qua thủy tinh hoặc trong suốt với chùm tia laser.
3. Nó có thể hàn các vật liệu chịu lửa như titan và thạch anh, và cũng có thể hàn các vật liệu khác nhau với kết quả tốt.
4. Sau khi tia laser được tập trung, mật độ năng lượng cao. Tỷ lệ khung hình có thể đạt tới 5:1 và có thể đạt tới 10:1 khi hàn các thiết bị công suất cao.
5. Có thể thực hiện hàn vi mô. Sau khi chùm tia laser được tập trung, có thể thu được một điểm nhỏ và có thể định vị chính xác. Nó có thể được áp dụng để lắp ráp và hàn các phôi gia công siêu nhỏ và nhỏ để đạt được sản xuất hàng loạt tự động.
6. Nó có thể hàn các khu vực khó tiếp cận và thực hiện hàn đường dài không tiếp xúc, rất linh hoạt. Đặc biệt trong những năm gần đây, công nghệ xử lý laser YAG đã áp dụng công nghệ truyền dẫn cáp quang, giúp công nghệ hàn laser được quảng bá và ứng dụng rộng rãi hơn.
7. Chùm tia laser dễ dàng phân chia theo thời gian và không gian, đồng thời có thể xử lý nhiều chùm tia tại nhiều vị trí, tạo điều kiện để hàn chính xác hơn.
Khuyết điểm:
1. Yêu cầu độ chính xác lắp ráp của phôi phải cao và vị trí của chùm tia trên phôi không thể bị lệch đáng kể. Điều này là do kích thước điểm laser sau khi lấy nét nhỏ và đường hàn hẹp, gây khó khăn cho việc thêm vật liệu kim loại phụ. Nếu độ chính xác lắp ráp của phôi hoặc độ chính xác định vị của dầm không đáp ứng yêu cầu thì dễ xảy ra khuyết tật hàn.
2. Chi phí của tia laser và các hệ thống liên quan cao và số tiền đầu tư một lần lớn.
Các lỗi hàn laser thường gặptrong sản xuất pin lithium
1. Độ xốp hàn
Những khiếm khuyết thường gặp ởhàn laserlà lỗ chân lông. Bể nóng chảy hàn sâu và hẹp. Trong quá trình hàn laser, nitơ xâm nhập vào bể nóng chảy từ bên ngoài. Trong quá trình làm nguội và hóa rắn kim loại, độ hòa tan của nitơ giảm khi nhiệt độ giảm. Khi kim loại nóng chảy nguội đi và bắt đầu kết tinh, độ hòa tan sẽ giảm mạnh và đột ngột. Lúc này một lượng lớn khí sẽ kết tủa tạo thành bong bóng. Nếu tốc độ nổi của bong bóng nhỏ hơn tốc độ kết tinh kim loại sẽ tạo ra các lỗ xốp.
Trong các ứng dụng trong ngành công nghiệp pin lithium, chúng ta thường thấy rằng lỗ chân lông đặc biệt dễ xảy ra trong quá trình hàn điện cực dương, nhưng hiếm khi xảy ra trong quá trình hàn điện cực âm. Điều này là do điện cực dương được làm bằng nhôm và điện cực âm được làm bằng đồng. Trong quá trình hàn, nhôm lỏng trên bề mặt đã ngưng tụ trước khi khí bên trong tràn ra hoàn toàn, ngăn không cho khí tràn ra và tạo thành các lỗ lớn nhỏ. Khí khổng nhỏ.
Ngoài các nguyên nhân gây ra lỗ chân lông nêu trên, lỗ chân lông còn bao gồm không khí ngoài trời, độ ẩm, dầu bề mặt,… Ngoài ra, hướng và góc thổi nitơ cũng sẽ ảnh hưởng đến sự hình thành lỗ chân lông.
Làm thế nào để giảm sự xuất hiện của lỗ chân lông hàn?
Đầu tiên, trướchàn, các vết dầu và tạp chất trên bề mặt của vật liệu đến cần được làm sạch kịp thời; trong quá trình sản xuất pin lithium, việc kiểm tra nguyên liệu đầu vào là một quá trình thiết yếu.
Thứ hai, lưu lượng khí bảo vệ phải được điều chỉnh theo các yếu tố như tốc độ hàn, công suất, vị trí, v.v., không quá lớn cũng không quá nhỏ. Áp suất áo choàng bảo vệ phải được điều chỉnh theo các yếu tố như công suất laser và vị trí lấy nét, đồng thời không được quá cao cũng không quá thấp. Hình dạng của vòi phun áo choàng bảo vệ phải được điều chỉnh theo hình dạng, hướng và các yếu tố khác của mối hàn để áo choàng bảo vệ có thể bao phủ đều khu vực hàn.
Thứ ba, kiểm soát nhiệt độ, độ ẩm và bụi trong không khí trong nhà xưởng. Nhiệt độ và độ ẩm xung quanh sẽ ảnh hưởng đến độ ẩm trên bề mặt chất nền và khí bảo vệ, từ đó sẽ ảnh hưởng đến việc tạo ra và thoát hơi nước trong bể nóng chảy. Nếu nhiệt độ và độ ẩm môi trường quá cao, sẽ có quá nhiều độ ẩm trên bề mặt nền và khí bảo vệ, tạo ra một lượng hơi nước lớn, dẫn đến lỗ chân lông. Nếu nhiệt độ và độ ẩm môi trường quá thấp sẽ có quá ít độ ẩm trên bề mặt nền và trong khí bảo vệ, làm giảm sự sinh ra hơi nước, từ đó làm giảm lỗ chân lông; để nhân viên chất lượng phát hiện giá trị mục tiêu của nhiệt độ, độ ẩm và bụi tại trạm hàn.
Thứ tư, phương pháp xoay chùm tia được sử dụng để thu nhỏ hoặc loại bỏ các lỗ rỗng trong hàn xuyên sâu bằng laser. Do có thêm chuyển động lắc trong quá trình hàn, chuyển động tịnh tiến của chùm tia tới đường hàn gây ra sự nóng chảy lặp đi lặp lại của một phần đường hàn, giúp kéo dài thời gian lưu trú của kim loại lỏng trong bể hàn. Đồng thời, độ lệch của chùm tia cũng làm tăng lượng nhiệt đầu vào trên một đơn vị diện tích. Tỷ lệ chiều sâu và chiều rộng của mối hàn giảm, tạo điều kiện cho sự xuất hiện của bong bóng, từ đó loại bỏ lỗ chân lông. Mặt khác, sự chuyển động của chùm tia làm cho lỗ nhỏ dao động tương ứng, điều này còn có thể tạo ra lực khuấy cho bể hàn, tăng độ đối lưu và khuấy trộn của bể hàn, đồng thời có tác dụng loại bỏ các lỗ rỗng.
Thứ năm, tần số xung, tần số xung đề cập đến số xung phát ra từ chùm tia laser trên một đơn vị thời gian, điều này sẽ ảnh hưởng đến lượng nhiệt đầu vào và sự tích tụ nhiệt trong bể nóng chảy, sau đó ảnh hưởng đến trường nhiệt độ và trường dòng chảy trong bể nóng chảy. hồ bơi. Nếu tần số xung quá cao sẽ dẫn đến lượng nhiệt đầu vào quá mức trong bể nóng chảy, khiến nhiệt độ của bể nóng chảy quá cao, tạo ra hơi kim loại hoặc các nguyên tố khác dễ bay hơi ở nhiệt độ cao, dẫn đến hình thành lỗ chân lông. Nếu tần số xung quá thấp sẽ dẫn đến tích tụ nhiệt trong bể nóng chảy không đủ, khiến nhiệt độ của bể nóng chảy quá thấp, làm giảm độ hòa tan và thoát khí, dẫn đến hình thành lỗ chân lông. Nói chung, tần số xung phải được chọn trong phạm vi hợp lý dựa trên độ dày lớp nền và công suất laser, đồng thời tránh quá cao hoặc quá thấp.
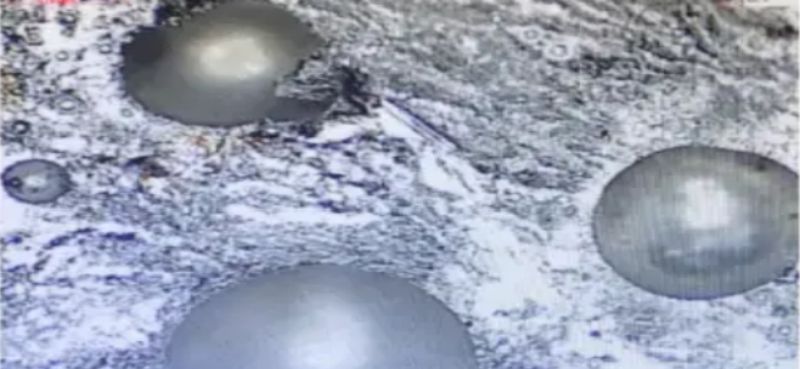
Hàn lỗ (hàn laser)
2. Vết hàn
Các tia bắn tung tóe sinh ra trong quá trình hàn, hàn laser sẽ ảnh hưởng nghiêm trọng đến chất lượng bề mặt của mối hàn, gây ô nhiễm và hư hỏng thấu kính. Hiệu suất chung như sau: sau khi hoàn thành hàn laser, nhiều hạt kim loại xuất hiện trên bề mặt vật liệu hoặc phôi và bám vào bề mặt vật liệu hoặc phôi. Hiệu suất trực quan nhất là khi hàn ở chế độ điện kế, sau một thời gian sử dụng thấu kính bảo vệ của điện kế, trên bề mặt sẽ xuất hiện những vết rỗ dày đặc, những vết rỗ này là do vết hàn gây ra. Sau một thời gian dài sẽ dễ cản trở ánh sáng, đèn hàn sẽ có vấn đề dẫn đến hàng loạt vấn đề như đứt mối hàn, hàn ảo.
Nguyên nhân gây ra hiện tượng bắn tung tóe là gì?
Đầu tiên, mật độ năng lượng, mật độ năng lượng càng lớn thì càng dễ tạo ra tia lửa và sự bắn tung tóe có liên quan trực tiếp đến mật độ năng lượng. Đây là một vấn đề thế kỷ. Ít nhất cho đến nay ngành này vẫn chưa giải quyết được vấn đề bắn tung tóe, chỉ có thể nói là đã giảm bớt một chút. Trong ngành công nghiệp pin lithium, bắn tung tóe là thủ phạm lớn nhất gây ra hiện tượng đoản mạch pin, nhưng vẫn chưa thể giải quyết được nguyên nhân gốc rễ. Tác động của vết bắn lên pin chỉ có thể được giảm bớt từ quan điểm bảo vệ. Ví dụ, một vòng tròn gồm các cổng loại bỏ bụi và vỏ bảo vệ được thêm vào xung quanh bộ phận hàn và các hàng dao hơi được thêm vào thành vòng tròn để ngăn tác động của tia bắn hoặc thậm chí làm hỏng pin. Việc hủy hoại môi trường, sản phẩm, linh kiện xung quanh trạm hàn có thể nói là đã cạn kiệt phương tiện.
Về việc giải quyết vấn đề bắn tóe, chỉ có thể nói rằng việc giảm năng lượng hàn giúp giảm bắn tóe. Giảm tốc độ hàn cũng có thể hữu ích nếu độ xuyên thấu không đủ. Nhưng trong một số yêu cầu quy trình đặc biệt, nó có rất ít tác dụng. Đó là cùng một quy trình, các máy móc khác nhau và các lô vật liệu khác nhau có tác dụng hàn hoàn toàn khác nhau. Vì vậy, có một quy luật bất thành văn trong ngành năng lượng mới, đó là một bộ thông số hàn cho một thiết bị.
Thứ hai, nếu bề mặt của vật liệu hoặc phôi đã qua xử lý không được làm sạch, vết dầu hoặc chất ô nhiễm cũng sẽ gây ra hiện tượng bắn tung tóe nghiêm trọng. Lúc này, việc dễ dàng nhất là làm sạch bề mặt của vật liệu đã qua xử lý.
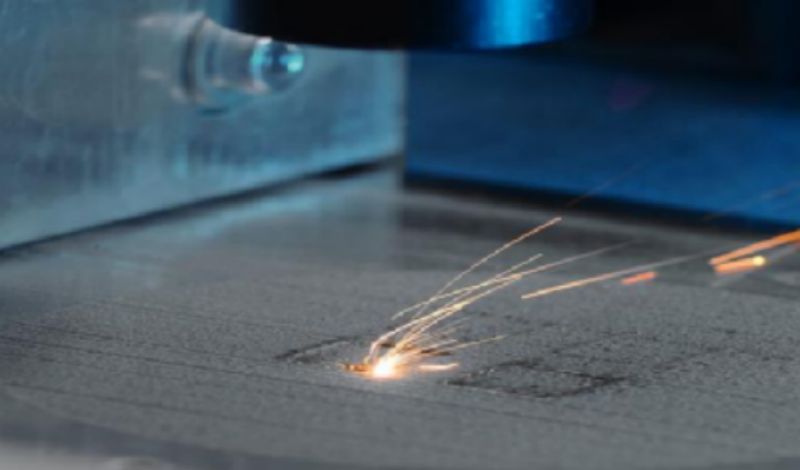
3. Độ phản xạ cao của hàn laser
Nói chung, độ phản xạ cao đề cập đến thực tế là vật liệu xử lý có điện trở suất nhỏ, bề mặt tương đối mịn và tốc độ hấp thụ thấp đối với tia laser cận hồng ngoại, dẫn đến lượng phát xạ laser lớn và bởi vì hầu hết các tia laser đều được sử dụng. theo chiều dọc Do vật liệu hoặc một lượng nghiêng nhỏ, ánh sáng laser quay trở lại đi vào đầu đầu ra và thậm chí một phần ánh sáng quay trở lại được ghép vào sợi truyền năng lượng và được truyền ngược dọc theo sợi vào bên trong của tia laser, làm cho các thành phần cốt lõi bên trong tia laser tiếp tục ở nhiệt độ cao.
Khi độ phản xạ quá cao trong quá trình hàn laser, có thể thực hiện các giải pháp sau:
3.1 Sử dụng lớp phủ chống phản chiếu hoặc xử lý bề mặt vật liệu: phủ lên bề mặt vật liệu hàn một lớp phủ chống phản chiếu có thể làm giảm hiệu quả độ phản xạ của tia laser. Lớp phủ này thường là vật liệu quang học đặc biệt có độ phản xạ thấp giúp hấp thụ năng lượng laser thay vì phản xạ lại. Trong một số quy trình, chẳng hạn như hàn bộ thu dòng điện, kết nối mềm, v.v., bề mặt cũng có thể được dập nổi.
3.2 Điều chỉnh góc hàn: Bằng cách điều chỉnh góc hàn, chùm tia laser có thể chiếu tới vật liệu hàn ở góc thích hợp hơn và giảm hiện tượng phản xạ. Thông thường, để chùm tia laser tới vuông góc với bề mặt vật liệu được hàn là một cách tốt để giảm phản xạ.
3.3 Thêm chất hấp thụ phụ: Trong quá trình hàn, một lượng chất hấp thụ phụ nhất định như bột hoặc chất lỏng được thêm vào mối hàn. Những chất hấp thụ này hấp thụ năng lượng laser và làm giảm độ phản xạ. Chất hấp thụ thích hợp cần được lựa chọn dựa trên vật liệu hàn cụ thể và các tình huống ứng dụng. Trong ngành công nghiệp pin lithium, điều này khó xảy ra.
3.4 Dùng sợi quang để truyền tia laser: Nếu có điều kiện có thể dùng sợi quang để truyền tia laser đến vị trí hàn để giảm độ phản xạ. Sợi quang có thể dẫn tia laser tới khu vực hàn để tránh tiếp xúc trực tiếp với bề mặt vật liệu hàn và giảm sự xuất hiện của phản xạ.
3.5 Điều chỉnh các thông số laser: Bằng cách điều chỉnh các thông số như công suất laser, tiêu cự và đường kính tiêu cự, có thể kiểm soát sự phân bố năng lượng laser và giảm phản xạ. Đối với một số vật liệu phản chiếu, việc giảm công suất laser có thể là một cách hiệu quả để giảm phản xạ.
3.6 Sử dụng bộ tách chùm: Bộ tách chùm có thể dẫn một phần năng lượng laser vào thiết bị hấp thụ, nhờ đó làm giảm sự xuất hiện của phản xạ. Thiết bị tách chùm tia thường bao gồm các bộ phận quang học và bộ hấp thụ, và bằng cách chọn các bộ phận thích hợp và điều chỉnh cách bố trí của thiết bị, có thể đạt được độ phản xạ thấp hơn.
4. Hàn undercut
Trong quy trình sản xuất pin lithium, quy trình nào có nhiều khả năng gây ra hiện tượng cắt xén hơn? Tại sao lại xảy ra hiện tượng undercut? Hãy phân tích nó.
Undercut, nhìn chung các nguyên liệu hàn không kết hợp tốt với nhau, khe hở quá lớn hoặc xuất hiện rãnh, chiều sâu và chiều rộng về cơ bản lớn hơn 0,5mm, tổng chiều dài lớn hơn 10% chiều dài mối hàn, hoặc lớn hơn tiêu chuẩn quy trình sản phẩm với độ dài được yêu cầu.
Trong toàn bộ quá trình sản xuất pin lithium, hiện tượng cắt xén có nhiều khả năng xảy ra hơn và nó thường được phân bố trong quá trình hàn trước và hàn kín tấm bìa hình trụ và hàn trước và hàn kín tấm bìa vỏ nhôm vuông. Nguyên nhân chính là do tấm bìa bịt kín cần phối hợp với vỏ để hàn, quá trình ăn khớp giữa tấm bìa bịt kín và vỏ dễ bị tạo ra các khe hở mối hàn quá mức, rãnh, sập, v.v. nên đặc biệt dễ bị khoét mép .
Vậy nguyên nhân gây ra undercut là gì?
Nếu tốc độ hàn quá nhanh, kim loại lỏng phía sau lỗ nhỏ hướng vào tâm mối hàn sẽ không có thời gian để phân bố lại dẫn đến hiện tượng đông đặc và cắt rãnh hai bên mối hàn. Trước tình hình trên, chúng ta cần tối ưu hóa các thông số hàn. Nói một cách đơn giản, đó là các thử nghiệm lặp lại để xác minh các thông số khác nhau và tiếp tục thực hiện DOE cho đến khi tìm thấy các thông số thích hợp.
2. Vật liệu hàn có quá nhiều khe hở, rãnh, xẹp, v.v.. của vật liệu hàn sẽ làm giảm lượng kim loại nóng chảy lấp đầy các khe hở, dễ xảy ra hiện tượng undercut. Đây là vấn đề về thiết bị và nguyên liệu thô. Liệu nguyên liệu hàn có đáp ứng được yêu cầu nguyên liệu đầu vào của quy trình của chúng tôi hay không, liệu độ chính xác của thiết bị có đáp ứng yêu cầu hay không, v.v. Thông lệ là liên tục tra tấn và đánh đập các nhà cung cấp cũng như những người phụ trách thiết bị.
3. Nếu năng lượng giảm quá nhanh khi kết thúc quá trình hàn laser, lỗ nhỏ có thể bị xẹp xuống, dẫn đến hiện tượng khoét lõm cục bộ. Sự kết hợp chính xác giữa sức mạnh và tốc độ có thể ngăn chặn hiệu quả việc hình thành các vết cắt. Như người xưa vẫn nói, hãy lặp lại các thử nghiệm, xác minh các tham số khác nhau và tiếp tục DOE cho đến khi bạn tìm thấy các tham số phù hợp.
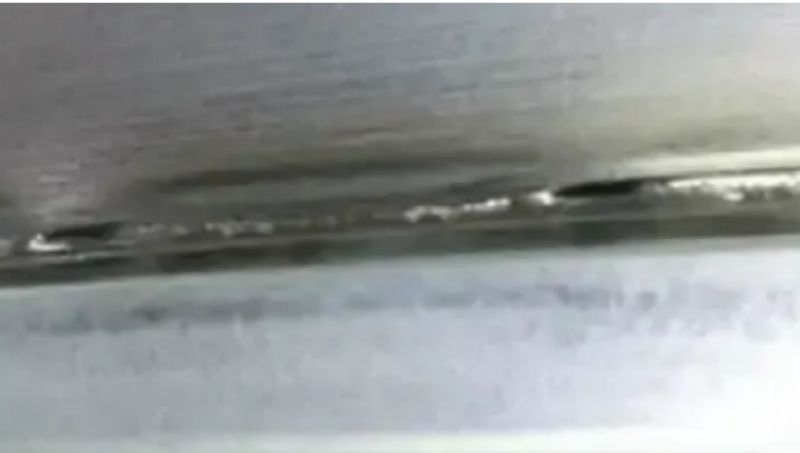
5. Sụp đổ trung tâm hàn
Nếu tốc độ hàn chậm thì vũng nóng chảy sẽ lớn và rộng hơn, làm tăng lượng kim loại nóng chảy. Điều này có thể làm cho việc duy trì sức căng bề mặt trở nên khó khăn. Khi kim loại nóng chảy trở nên quá nặng, tâm mối hàn có thể chìm xuống và tạo thành các vết rỗ. Trong trường hợp này, mật độ năng lượng cần phải được giảm đi một cách thích hợp để ngăn chặn sự sụp đổ của bể tan chảy.
Trong một tình huống khác, khe hở hàn chỉ tạo thành sự xẹp xuống mà không gây thủng. Đây chắc chắn là vấn đề về sự phù hợp của thiết bị.
Sự hiểu biết đúng đắn về các khuyết tật có thể xảy ra trong quá trình hàn laser và nguyên nhân của các khuyết tật khác nhau cho phép đưa ra cách tiếp cận có mục tiêu hơn để giải quyết mọi vấn đề hàn bất thường.
6. Vết nứt hàn
Các vết nứt xuất hiện trong quá trình hàn laser liên tục chủ yếu là các vết nứt nhiệt, chẳng hạn như vết nứt tinh thể và vết nứt hóa lỏng. Nguyên nhân chính gây ra các vết nứt này là do lực co ngót lớn do mối hàn tạo ra trước khi nó đông đặc hoàn toàn.
Ngoài ra còn có những lý do sau gây ra vết nứt khi hàn laser:
1. Thiết kế mối hàn không hợp lý: Việc thiết kế hình dạng và kích thước mối hàn không đúng có thể gây ra sự tập trung ứng suất hàn, từ đó gây ra các vết nứt. Giải pháp là tối ưu hóa thiết kế mối hàn để tránh tập trung ứng suất hàn. Bạn có thể sử dụng các mối hàn offset thích hợp, thay đổi hình dạng mối hàn, v.v.
2. Thông số hàn không khớp: Việc lựa chọn thông số hàn không đúng, chẳng hạn như tốc độ hàn quá nhanh, công suất quá cao, v.v., có thể dẫn đến sự thay đổi nhiệt độ không đồng đều trong khu vực hàn, dẫn đến ứng suất hàn và vết nứt lớn. Giải pháp là điều chỉnh các thông số hàn phù hợp với vật liệu và điều kiện hàn cụ thể.
3. Chuẩn bị bề mặt hàn kém: Việc không làm sạch và xử lý trước bề mặt hàn đúng cách như loại bỏ oxit, dầu mỡ, v.v. sẽ ảnh hưởng đến chất lượng và độ bền của mối hàn và dễ dẫn đến các vết nứt. Giải pháp là làm sạch và xử lý trước bề mặt hàn đầy đủ để đảm bảo các tạp chất, chất gây ô nhiễm trong khu vực hàn được xử lý hiệu quả.
4. Kiểm soát nhiệt đầu vào hàn không đúng cách: Kiểm soát kém lượng nhiệt đầu vào trong quá trình hàn, chẳng hạn như nhiệt độ quá cao trong quá trình hàn, tốc độ làm mát của lớp hàn không đúng, v.v., sẽ dẫn đến thay đổi cấu trúc của khu vực hàn, dẫn đến các vết nứt . Giải pháp là kiểm soát nhiệt độ và tốc độ làm nguội trong quá trình hàn để tránh hiện tượng quá nhiệt và nguội nhanh.
5. Giảm ứng suất không đủ: Xử lý giảm ứng suất không đủ sau khi hàn sẽ dẫn đến giảm ứng suất không đủ ở khu vực hàn, dễ dẫn đến các vết nứt. Giải pháp là thực hiện xử lý giảm ứng suất thích hợp sau khi hàn, chẳng hạn như xử lý nhiệt hoặc xử lý rung (lý do chính).
Đối với quy trình sản xuất pin lithium, quy trình nào dễ gây ra vết nứt hơn?
Nói chung, các vết nứt dễ xảy ra trong quá trình hàn kín, chẳng hạn như hàn kín vỏ thép hình trụ hoặc vỏ nhôm, hàn kín vỏ nhôm vuông, v.v. Ngoài ra, trong quá trình đóng gói mô-đun, việc hàn bộ thu dòng điện cũng dễ xảy ra. đến các vết nứt.
Tất nhiên, chúng ta cũng có thể sử dụng dây hàn, làm nóng trước hoặc các phương pháp khác để giảm hoặc loại bỏ những vết nứt này.
Thời gian đăng: Sep-01-2023